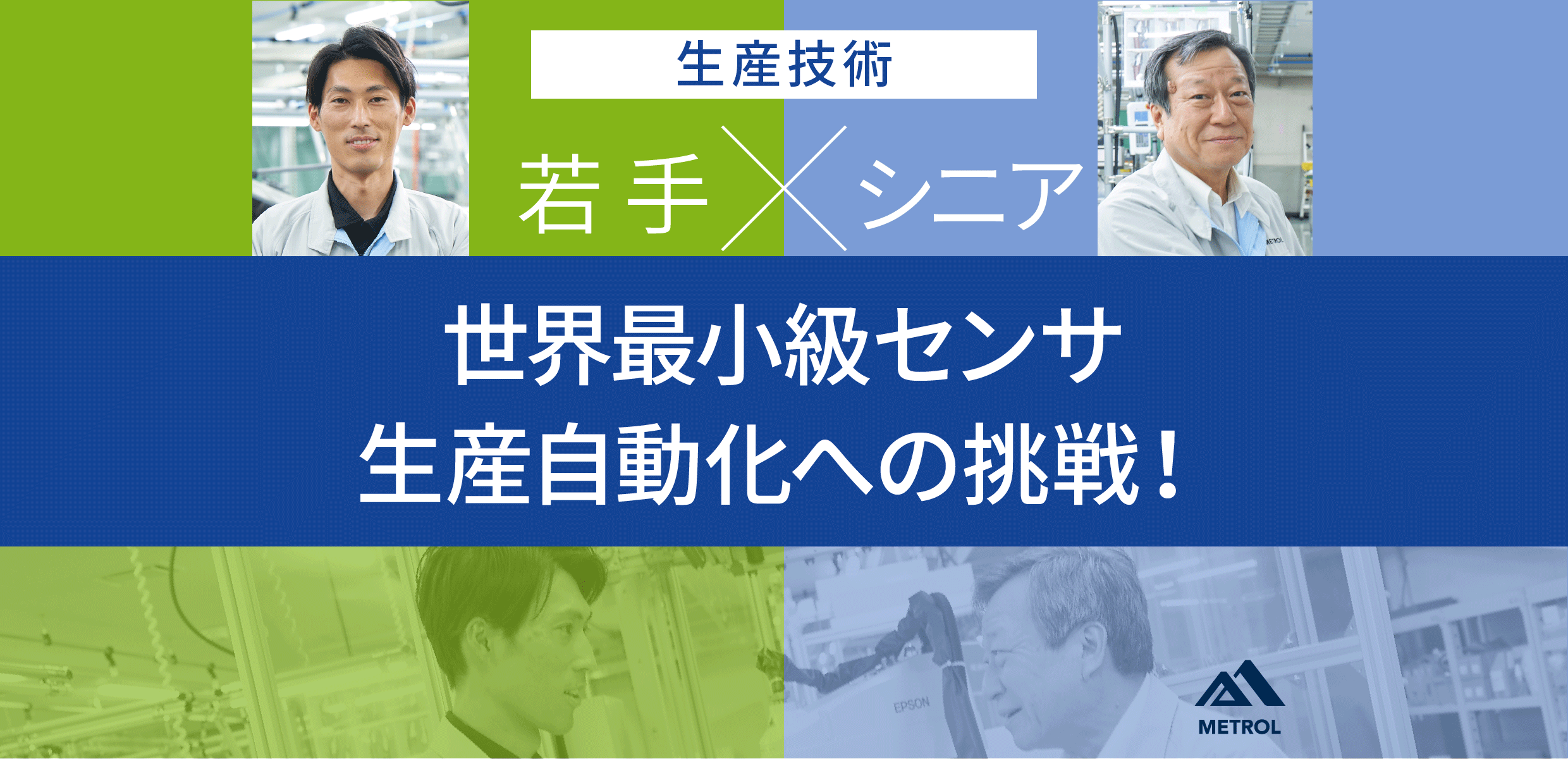
若手×シニア|生産技術者が挑む!世界最小級センサの生産自動化への道のりとは?
プロジェクト概要
直径5mm、長さ17mmの世界最小級センサ「PT小型タッチセンサ*(以下:PTスイッチ)』。(* PT:Precision Touch switchの頭文)
超小型・高精度のこのセンサは、PCやスマートフォンの半導体、医療機器など、幅広い業界の製造現場で使われているメトロールの主力製品です。近年、アメリカ・ヨーロッパを中心に売上急上昇中のヒット商品です。
身の回りのモノがどんどん小型化され、同時にモノをつくる機械にも小型化・高精度化が求められていることもあり、この世界最小級のセンサの需要が増えています。
そんなPTスイッチですが、実はベテラン職人の緻密な手作業で組み立てられているのです。超小型のPTスイッチを組み立てるのは至難の業。本プロジェクトでは、ベテラン職人の手作業でしか成しえなかった世界最小級センサの、組み立て自動化に挑戦した「生産技術エンジニア」の開発秘話をご紹介します。
- テーマ
- PTタッチスイッチ自動組み立て機の導入プロジェクト
- PJメンバー
- 2名
- PJ期間
- 約3年
- 担当業務
- リーダー:生産技術開発部 八丁
メンバー:生産技術開発部 中田
目次
「生産技術」は、製品の量産体制を支える仕事
生産技術部のKJです。みなさんは「生産技術」がどんな仕事か知っていますか?
「生産技術」は、良いモノを効率よくたくさん作るにはどんな仕組みが理想的か?をひたすら考える人達です。
具体的には製品をどんな手順でつくって、どんな設備が必要か、を考えて量産体制を支える仕事とも言えます。
そのアプローチは無限にあります。手でやっている作業を機械やロボットに置き換える「自動化」も選択肢の一つです。
例えば、製品を1日10個作るのが精一杯の状態で、お客様から「1日1000個つくってほしい」と依頼されたとします。
- 作る人を増やすのか
- 作り方を見直すのか
のように頑張りに頼らない作り方の工夫が必要です。お客様のもとに「高品質」「短納期」「低価格」で滞りなく製品を届けるには、こうした生産技術の役割が欠かせません。自動化が進むモノづくり業界で、年々重要性が増している仕事なんです。
僕の1番のミッションは、「製造現場の作業者がやりずらかったり、辛かったりする作業を楽にする事」だと思って仕事をしています。現場の声を一つ一つ解決することが、より生産性の高い生産ラインにつながって、結果的にお客様に還元されます。今回「自動組み立て機」(=以下、自動機)の開発・導入に挑戦したきっかけも、熟練作業者だけに負担が偏る状況をなんとか改善したい!と思ったことでした。
順調な製品の売れ行きに反して、生産が追いつかない!
「小型タッチセンサ」は販売が伸びる一方で、生産量が追い付かず販売を一時ストップする緊急事態が起きていました。
この製品にはゴマ粒ほどの極小部品を使用するため、組み立てには熟練技術と忍耐力が求められます。これまでこの熟練技術を持つのはベテラン作業者2名だけでした。しかも、この2人はスキルが高いため他の生産ラインでも引っ張りだこ。他の作業者を二人のレベルまで育てる時間の余裕もありませんでした。
僕には、この製品は今後もっと伸びてくるという感覚がありました。だから、ベテラン作業者だけに頼る現状を、昨日入社した新人でも組み立てができる、という状態にしたかったんです。こうして自動機開発に向けて動き出しました。
生産技術者は職人の通訳者!?
生産技術の仕事は、まず「購入仕様書」の作成から始まります。
「購入仕様書」とは、開発する設備に必要となる機能などを書いた「設計における羅針盤」。いかにクオリティの高い購入仕様書を作れるかが自動機の成功を左右します。
仕様書のレベル=生産技術者の技量を測るバロメータと言っても過言ではありません!
この購入仕様書には
- 自動化したい工程の図面
- 部品を組み立てるときの条件(角度や使用する力など)
- 1台組み立てるのにかかる時間 ・最終的なアウトプット(成果物)の品質
などが書かれています。
このとき生産技術者は、専門知識を持たない作業者の「通訳者」となります。
作業者がこれまで勘で行っていた手作業を、僕らが数値データなど具体的な条件に変換して購入仕様書に落とし込みます。
設備製造の社外パートナー探し
次に購入仕様書をもとに、生産設備を製造してくれる機械メーカーを探します。
「作業が細かいうえに、要求する精度が厳しすぎる」
生産設備を得意とする機械メーカー6社に話を持ちかけましたが、設計の難しさを理由に白旗をあげる案件でした。
そんな中、「こんなに難しい案件は創業以来はじめて」としながらも、1社が受注してくれました。パートナーが見つかり共同開発がスタートします。
直径が同じ「穴」と「ピン」。ロボットが一発で差し込むには?
機械メーカーに自動機の開発状況を確認すると、装置の構造を根本から見直すことになる重大な課題が見つかりました。製品の精度を左右する最も重要な「穴の空いた部品に、ピンをはめ込む工程」で不具合が起きていたのです。
穴とピンの直径はほぼ同じ。2つの部品を組み合わせるために必要な精度は10µm(*)、これ以上位置がずれると不良品になってしまいます。
(* 10µm:髪の毛の太さが50μmなのでその5分の1のズレ。)

職人による手作業ならば、位置が少しずれても手の感覚と目視で微調整が可能でした。この調整の塩梅こそが「職人技」でした。しかし自動機では、人手のような調整機能はありません。ロボットは狙いを定めて一発でピンを穴に差し込まなければなりません。
当初、装置メーカーの仮説はこうでした。
- 動きの再現性の高いロボットなら正確にピンと穴の位置を決めて入れられる
- 座標を定めれば毎回同じ位置にピンを持ってくることができる
- 動きが正確なメカであればピンを穴に確実に入れられる
しかし実際には、仮説通りの結果にはなりませんでした。
ロボットが正確に動いても、停止時の振動で誤差が生まれて部品の組み立てがずれてしまうのです。
シニアエンジニアの知識も借りて導き出された解決策
悩んだ末に、振動で誤差が生じても「ピン先の位置調整」ができる方法にたどり着きます。それが
「画像認識」技術でガイドの穴位置を検出する
提案したのは、シニア採用で中途入社した中田さんでした。僕のアドバイザーでもある中田さんは、以前、画像認識をつかった設備設計の経験がありました。要求する精度を達成するには、画像認識しかないと確信していたそうです。
中田「画像認識で穴位置を検出したうえで、ピンの先端も同じように画像認識で見ていれば、ずれずに確実に入れられるでしょ。」
メトロールが「画像認識技術」を導入するのは初めての試みでした。
納得するまでとことん意見交換 大改造へ突き動かした熱意
僕と中田さんは、装置メーカーと直接意見を交わすために先方の工場に3週間も泊まりこみました。先方は当初の仮説通りロボットの動きだけで課題をクリアしたいと主張しましたが、議論の末、僕らの提案した「画像認識で位置を検出する方法」が採用されました。製品の精度に関わる重要な部分でしたから、絶対に譲れない僕らの熱意が伝わったと思っています。
完成間近の自動機の大改造となり開発時期が伸びてしまいましたが、「画像認識」技術で自動機の精度が安定し、不良品の問題は一気に解決されました。
僕たちは世界一の精度のセンサをつくりたいんです。そのためには装置メーカーとセンサーメーカーがお互いのノウハウを出し合って課題を解決することがパートナーシップを組む上で重要です。
他社の工場で、自社の製品を大量生産!??
さらに最終段階では、センサの生産ラインを丸ごと装置メーカーの工場で再現するという力技を実行しました。自社の設備をトラックで輸送し、作業者もひきつれての大がかりなものになりました。
それぞれの工程で基準をクリアしていても、完成品になってから品質問題がみつかるという事態を防ぐためです。
装置メーカーの工場でタッチセンサの本番さながらの量産シミュレーションをさせてもらいました。こうして自動設備の試作品の品質を確認しながら、設備の最終調整に明け暮れました。
そして、自動機の設計スタートから約3年、世界で唯一のオーダーメイド装置「PTタッチセンサ自動組み立て機」がついに完成します。妥協しない設計が功を奏してたくさんのメリットが実現されました。
- 生産能力が3倍にアップ
- 手作業でつくったセンサよりも品質が向上した
- ベテラン作業者が負担の大きい作業から解放された。
- ベテランでなくても簡単操作で誰でも高精度な製品作れるようになった。
自動化によって、生産量が単純に増えるだけでなく、働く人の負担や製品の品質にもメリットが生まれるのが生産技術の醍醐味です。今後、販売数が増えても世界中のお客様を待たせることなく製品を届けることができるようになりました。
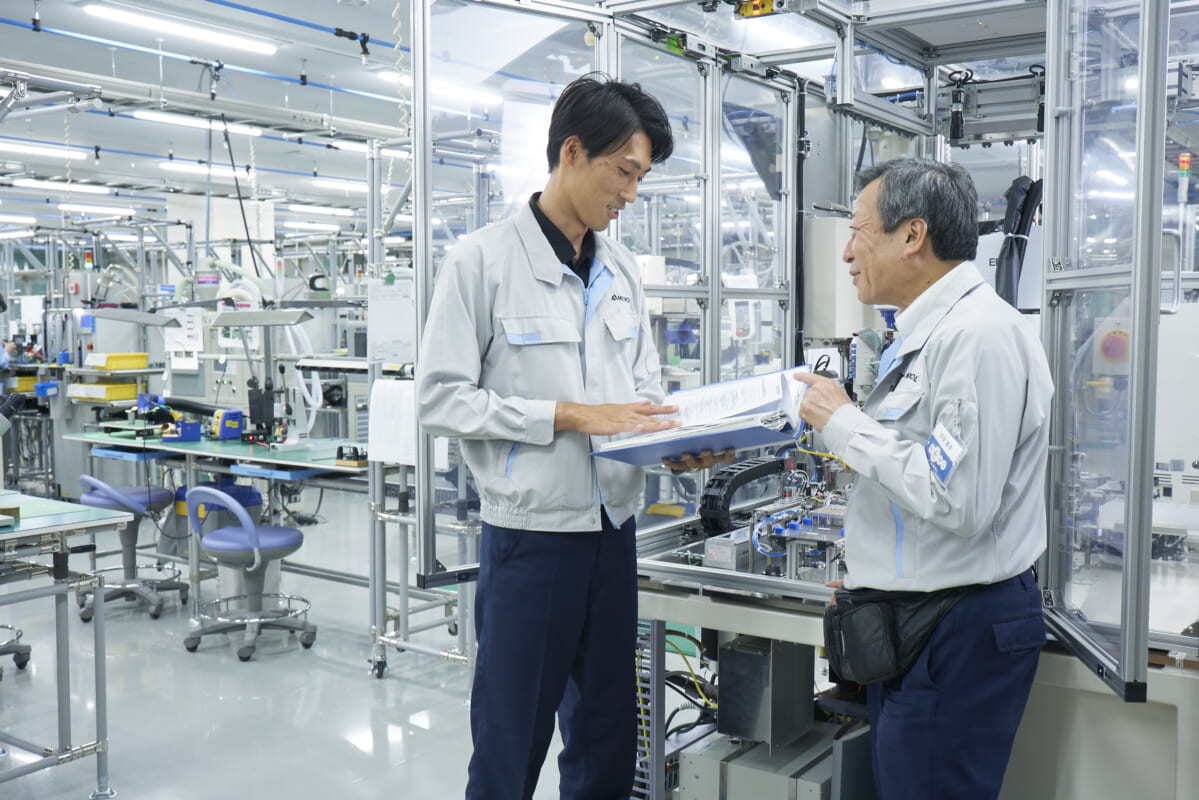
どうやってビジネスパートナーと信頼関係を築くか
様々な技術的な課題を乗り越えて、完成までたどり着いた今回のプロジェクト。
僕にとって一番の収穫は、ビジネスパートナーと信頼関係の築き方を身をもって経験できたことですね。
本来ならば、発注した後はメーカーに任せて、完成を待つのが一般的です。
しかし、今回は機械メーカーに長期間滞在して議論を交わしたり、自社の製造ラインを丸々持ち込んだりしました。自動機の開発を丸投げすることなく、機械メーカーと一緒に課題に取り組みました。
このやり方は、エンジニアとしての経験豊富なナカッサンのアドバイスによるものでした。
お互い技術で食ってる会社だからこそ、こだわりもあるし、得意な分野も違います。中田さんには「はじめからがっつり相手の組織に入って一緒になってやらないと絶対に完成しないよ」と言われていましたが、本当にその通りでした。
自分たちが大切に考えていることは主張しつつ、両社の間で落としどころを見つける。顧客とクライアントという壁を超えて、よい関係を育てていくことが重要です。
中田「顔を突き合わせて一緒に解決策を探す。このスタンスで昔からやってきて、結果として私は大概うまくいった。それは経験を重ねてわかってきたことです。自社の生産ラインをまるごと持って行ったのは初めてだったけどね。笑」
このプロジェクトを振り返ると、苦労はしたけど、自分の構想がカタチになるのはめちゃくちゃ楽しかったです。
装置を導入したことで、一番身近にいる作業者から「やりやすくなったよ」と感謝されることがなによりうれしいですね。
数ある方法の中から正解だろうと思うものを自分で手繰り寄せていくプロセスが、生産技術の一番の醍醐味だと思います。これからもいろいろなアプローチを挑戦していきたいですね。
メトロールでは一緒に働く仲間を探しています。
メトロールは生産設備や工作機械などの自動化に貢献するセンサーメーカーです。東京都立川市で作ったセンサは世界74ヶ国、7000社以上のお客様にご利用いただいています。次世代のものづくりや設備に使用されるユニークなセンサの企画から開発・製造までを一貫して行う開発型メーカーでもあります。
メトロールブランドを共に支え世界へ広めてくれる仲間を探しています! 少しでも興味を持っていただけた方は、メトロールまで気軽にご連絡ください。まずはカジュアル面談からという方でもOKです!